
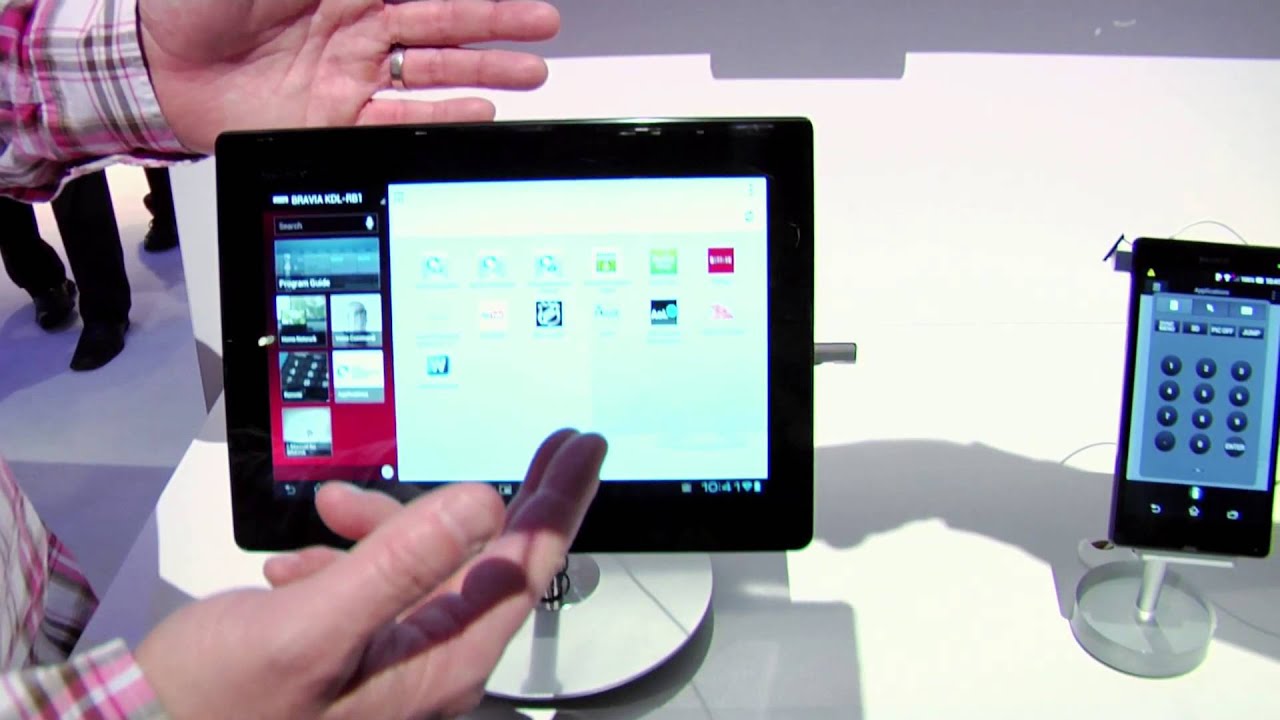
The 18,563.7102N force load is the bump, braking and cornering force generated when a vehicle is in motion and was obtained from ADAMS simulation model of McPherson Subaru suspension system. This is because the pinned ends of the tie rod were sliding and exhibiting instability when the load ( 18,563.7102N) was applied from one end whereas, the fixed-pinned ends behavior of the tie rod was fixed and stable under the applied force from the pinned-end. Under the influence of this force, the tie rod in pinned-pinned position gave a maximum buckling displacement of 0.0156133mm whereas, tie rod under the influence of the same force buckled with a maximum displacement of 27.5852mm.
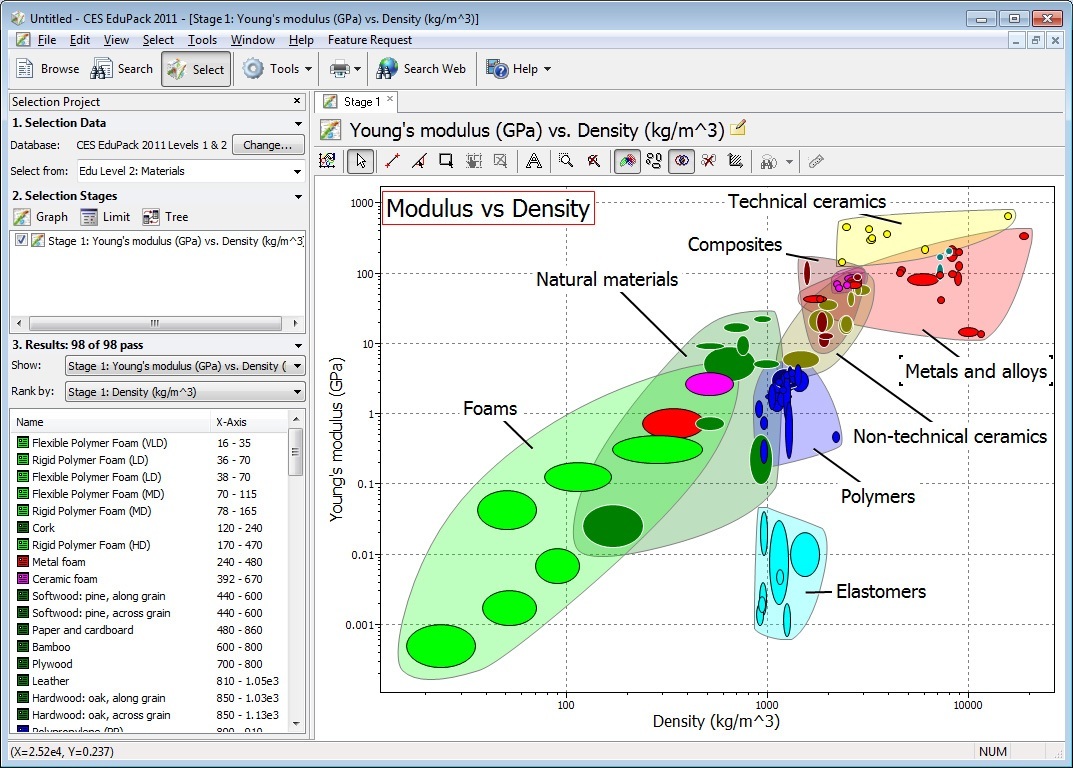
The tie rod was designed using SOLIDWORKS 2012 version and static analysis was carried out to determine buckling displacements of a vehicle tie rod with a force of 18,563.7102N acting from each ends under pinned-pinned and fixed-pinned condition. In terms of material properties, a tie rod requires high value of modulus of elasticity for stiffness, high fracture toughness against cracks and wear, and high yield strength against fatigue, and these properties were found in low alloy steel which conventional tie rods are manufactured from.

but low alloy steel was chosen based on the low cost, stiffness and yield strength. CES EduPack 2013 database level 2 was used in material selection of the tie rod which showed possible materials such as Nickel alloys, titanium alloy, aluminium alloy, low alloy steel etc. Abstract: A vehicle tie rod manufactured with materials that can resist the vertical, lateral and horizontal forces acting on the suspension system when the car is in operation may last for a longer period of time provided the operating condition of the vehicle is such that, the tie rod material does not exceed its elastic limit.
